제조
축적된 첨단기술로 원자력연료 제조의 안전성 향상
우리 회사는 1989년부터 국내에서 소요되는 원자력연료를 생산 및 공급하고 있으며, 축적된 첨단 기술은 원자력연료 제조의 안전성을 더욱 향상 시키고 있습니다.
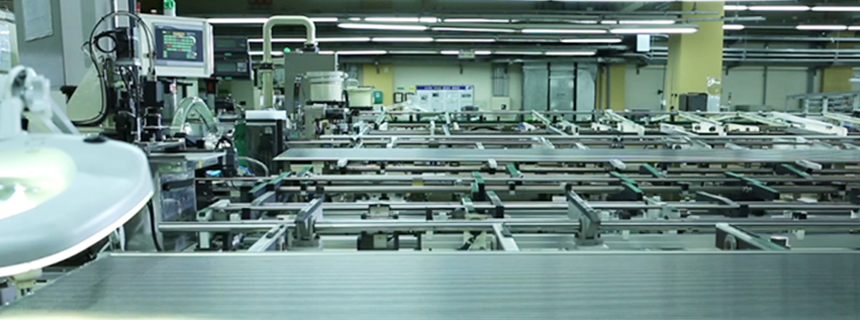
재변환 공정
부산항을 통해 입고된 우라늄은 재변환 공정을 통해 성형가공에 적합한 분말 상태의 우라늄으로 변환됩니다. 이때의 공정은 중앙제어실을 통한 24시간 모니터링과 현장 점검으로 엄격하게 관리·통제되고 있습니다. 또한, 각 공정별 자동제어 설정으로 설비의 오작동을 방지하고 공정 안전성을 확보하여 양질의 분말을 생산하고 있습니다.
소결체 제조 공정
재변환 공정에서 생산된 우라늄 분말은 틀에 채워져 절구 형태로 찍어진 후에 고온에서 도자기가 구워지듯 구워집니다. 그 후 표면을 갈아 일정한 크기로 만드는 공정을 거치면 연료봉 장입에 적합한 새끼손가락 손톱 크기의 5.2g 소결체로 탄생하게 됩니다. 이때 공정 작업자는 가운과 마스크, 장갑 등의 기본적인 장구 착용으로 제품 이물질 유입을 방지하고, 방사선안전 역시 확보할 수 있을 만큼 우라늄은 안전한 물질입니다. 또한, 소결체는 방사성 물질이 외부로 누출되는 것을 방지하는 다중방호 5벽 중 제1벽에 해당합니다.
피복관 제조 공정
제조된 소결체가 장입되는 피복관은 소결체에서 핵분열로 방출되는 열에너지를 냉각수에 전달하는 동시에 연소 시 발생하는 핵분열 생성물을 차폐시키는 제2의 방호벽 역할을 합니다. 피복관은 원자력발전소 노내의 고온, 고압 환경 하에서 열전달 특성이 뛰어나고, 내부식성이 매우 우수한 금속인 지르코늄합금으로 제조되며, 지르코늄합금은 핸드폰과 시계 케이스, 인공치아 등 우리 생활에 밀접하게 사용되는 안전한 금속입니다. 우리 회사는 2009년 지르코늄합금 피복관 국산화 개발에 성공하여 전량 자체 생산 중에 있으며, 해외 원자력 선진사에 수출할 만큼 제품의 안전성과 품질을 인정받고 있습니다.
연료봉 제조 공정
소결체와 스프링을 장입하고 헬륨가스를 충전한 후 봉단마개를 밀봉시킨 상태의 피복관을 연료봉이라고 합니다. 스프링은 핵분열시에 연료봉 내에서 생성되는 가스를 위한 공간을 확보하고 원자로 내 냉각수 순환에 의한 강한 흔들림으로부터 소결체의 흔들림을 방지하기 위해 장입되며, 헬륨가스는 원자로 내 높은 압력으로부터 연료봉의 파손을 막고 열분포를 균일하게 하기 위해 충전됩니다. 이렇게 제조된 연료봉 끝에는 각각의 바코드가 입력되어 있고 전산시스템으로 관리함으로써 연료봉에 문제 발생 시 빠른 추적과 조치를 가능하게 합니다.
품질검사 및 집합체 조립 공정
연료봉 제조 공정이 완료되면 후속 공정으로 이동하기에 앞서 총 3단계의 엄격한 품질검사가 실시됩니다. 이 때 샘플링이 아닌 전수검사를 시행하여 품질이 확실하게 검증된 연료봉만을 사용하여 안전성을 높이고 있습니다.
- 1단계 : 외부 손상 없이 내부를 검사하기 위한 비파괴 검사를 통해 우라늄 농축도, 소결 체 장입 길이와 간격, 스프링 장입 유무 등을 확인
- 2단계 : 가스누출시험기를 통해 연료봉 용접 부위의 결함 유무 확인
- 3단계 : 정밀 육안 검사를 통한 결함 유무 최종 확인
3단계의 품질검사를 마친 연료봉이 집합체로 조립된 후, 최종적으로 집합체의 길이, 직각도, 비틀림 등에 대한 검사가 수행되면 모든 원자력연료 제조 공정이 완료됩니다.
우리 회사는 숙련된 경험과 기술을 보유한 다수의 안전 및 품질관리전문가를 투입하여 각 공정별 최상의 안전과 품질을 확보하고 있습니다.